The Sèvres factory
Through this section, discover a specific know-how of a French heritage company with the highlighting: of a gesture, the tool to achieve it and the craftsman who executes it. The gesture, the tool, the actor.
At the gates of Paris. It is here, since the 18th century, that the Manufacture de Sèvres has worked to produce exceptional porcelain. If, over time, its premises have changed address several times, the practices of its art technicians have not changed. The proof…
Photo: Philippe Vaurès Santamaria
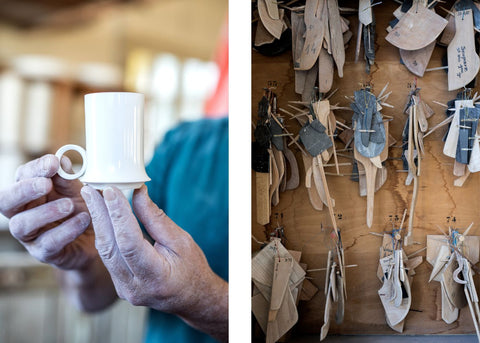
In the middle of a vertiginous hub of roads, the Manufacture de Sèvres goes almost unnoticed. And yet…Founded in 1740 in Vincennes, transferred in 1756 to the road to Versailles, then moved again, it has been based since 1876 on the banks of the Seine, at the edge of the Saint-Cloud estate, on a 4-hectare site. A maze of 24 buildings, housing the National Museum of Ceramics, a training center, a laboratory, a mill, 6 XXL wood ovens, production spaces... Because nothing escapes this cultural heritage classified as Historic Monuments.


The starting point of the turner's work. Clearly, a first shaping of the part to be made.
Porcelain paste in quantity, working drawing and tools required. Christian Boaretto has everything he needs at his fingertips. Slowly, surely, he shapes a small ball of dough which he flattens on the lathe, before working it by hand, raising it and lowering it. Precise, the operation is not trivial. It makes it possible to homogenize the material by removing its knots. The work can then really begin. Still on the lathe, the craftsman is busy giving the paste the overall exterior, then interior, shape of the object ordered. To go further, an unexpected tool intervenes. “The 'earth' preserves the memory of our gestures. If we are not careful, the porcelain restores these vibrations after firing. Hence the need to turn to… the sponge, to erase the imprints of his fingers. Another utensil to make its appearance: the ribs. Slate or wood, these shapes help to respect the curvature of the piece to be made. Quite quickly, its lines are drawn, but in a substantial thickness. This is how the design of the loom goes according to the Manufacture de Sèvres: a very basic outline responds, after a slight drying, to a long-term roughing. “Untreated, Sèvres porcelain is particularly soft. It doesn't allow very fine roughing…” One by one, Christian Boaretto arranges his roughings to his left. In a few days or even weeks, depending on their volume, they will be ready to be turned...
The tool: the tournassin
Behind this sharp metal blade mounted on a wooden handle, two other skills of the turner...
Starting with the very realization of the tool. It is the responsibility of the art technician himself. Christian Boaretto therefore regularly goes to the room in the Grand Atelier devoted to tools, to sharpen his swivels and even shape new ones. As his peers did before him. Because, over time, the object has not aged a bit. “He has remained the same for two and a half centuries! " And for good reason. It is essential to the second major phase of the turner's work: turning. Or how to roughen the draft of ⁴/₅ of its material to arrive at a part conforming to ¼ mm close to the working drawing. High precision work. Entirely manual, it therefore requires different tournassins, for the outside as well as the inside of the object, which its blades sculpt, on the lathe, by pouring out streams of dust and chips of "earth", with strident noises . Amazing. Just like the use of a pichouret. A kind of long wooden stick that Christian Boaretto carries on his shoulder and on which he presses the hand holding the tournassin, to better immobilize it and avoid, here again, untimely vibrations. In fact, the time for turning is not the same as that for roughing. The first is calculated in weeks, the other in days... Patience.
The actor: the turner
At 61, Christian Boaretto has accumulated 34 years of service within the Manufacture de Sèvres.
The meeting between these two happened quite fortuitously. He, the young graduate of the Beaux-Arts de Paris, passes the gate of the institution one day, out of curiosity. Very quickly, a workshop manager invited him to visit the premises. Christian Boaretto discovers the lathe, before deciding to make it his profession. There followed three years of training in the house school, a competition - so successful - and hundreds of porcelain pieces made by him. Without apparent weariness. How ? First of all, by varying the pleasures, between re-editions of old works and contemporary porcelain, small pieces and large sets... By starting to create in turn, on his own behalf, outside the establishment. And then, over time, if the techniques have evolved little or not at all, the relationship with the designers has changed. “With my decades of experience, I find it easier to accompany an artist in residence and to find, if necessary, viable solutions to the problems that arise. » The strength of age.